NobLog home
This one may give you deja vu - the feeling you've been here before. It certainly gives me that 'over and over' sensation.
One of my unfinished projects is that old Edwards Speedivac vacuum pump I'm restoring. Which stalled at the stage where I decided to build a vapor phase cleaning system to properly clean the parts before reassembly — and that is stuck waiting on my TIG welding capabilities to evolve out of primeval slime enough to seam weld thin stainless steel sheet. Which is dependent on... never mind. At least that one is not so important, as the old pump was just an exercise in antique restoration. Don't really need it. (But I do need the vapor phase cleaner, and the TIG skills for other things...)
Then there's the two driving trips I took to Melbourne earlier this year, in January, and June. Both well worth it, but I thought that was enough driving-madness for me this year.
Fate had other ideas. Something came up (important to me but not the topic here) and off I went to Melbourne yet again in August. Unlike previous trips that were very rushed this time I was able to stay a few days, party, meet old friends, etc. Of course it mostly rained. This trip's purpose had nothing to do with picking up vacuum equipment or electronics gear, however it did involve dropping in with my friend at his work a few times. Which naturally also meant a little spontaneous dumpster diving. And the inevitable ceremonial filling up the car with resulting space junk.
1. Couple of broken Motorola PTX760 VHF Trunked radios. Completely useless, just for pull-apart fun.
2. A 'blue thing'. Purely for curiosity and parts.
3. Akai 4000 'solid state' reel to reel tape player.
1. Javac DD 150 rotary vacuum pump, with 'failed electrical safety' tag.
2. Three card index cabinets, pretty full of cards.
3. Bag of little plastic vials, and box of assorted plumbing joints.
1. Very mysterious piece of gear, from India. What could it be for?
2. Slightly more practical looking "Hot Air Furnace" from the same Indian manufacturer.
3. Bundle of very large, very strong plastic bags.
4. Two flask heaters, rather battered and sad.
Guess which one this post is mainly about? Yeah, right, refurbishing another old vacuum pump. Except this time a pretty good one, and actually completed quickly. Amazing.
First though, lets get the stories of the other bits of junk out of the way.
The radios. My friend had found them dumpster-tossed a while ago, thought they might be repairable. Motorola make nice radios. Unfortunately these are VHF, not UHF — which all our other friends use for roadtrips, etc. But the killer is they are 'trunked', which means they only work with a base station. If they worked, which they don't. And the batteries are old NiMH and stuffed. So, dissection:
Pretty. It will be interesting to see if I can neatly desolder the shield cans without wrecking the PCB. I can have 16 attempts to get it right. Times two.
The 'blue thing' is actually a Samco 'UV & Ozone Dry Stripper'. It has a chamber with a hot plate in the bottom, and a UV light and ionized oxygen sprays in the top. Whatever you put in between those would not have a happy time. The thing had been heavily dropped into a dumpster, bending the case. It had also been stripped of some parts already, like the UV lamp and HV power supply for the oxygen ionizer. Still plenty of useful parts for me!
1. I never did take a photo of the thing's outside from the front, before stripping it. Oh well.
2. Well not quite as many useful parts as I thought. The whole thing is 100VAC internally, with a big gray 220V to 100V step-down transformer. So all those relay coils are 100V. Bah.
3. Ha ha. The wiring is almost all ridiculously oversize 14AWG for no reason. "Let's waste copper and make soldering connectors a pain", which makes me think this was designed by nubes. Also the wiring loom precision is well into OCD. They sure wanted to give the appearance of reliability. And yet while unwiring this connector block, one of the crimped lugs turned out to not be crimped properly. The bare wire end wasn't pushed into the wire-crimp part. Did this make the machine flakey? Maybe. I didn't bother to work out what this wire did.
4. Mainly what I wanted the thing for. Some nice stainless steel capillary fittings and solenoid valves, and a gas flow rate adjust and indicator. The solenoid coils are 100VAC, but can be replaced.
5. This too. A nice hotplate. Fortunately it has two 110V elements, that can be wired in series for 240VAC use. There's a setpoint controller that goes with it.
Above — The distilled haul: A hotplate and temp setpoint controller, a timer controller, some stainless and teflon tubing and fittings, buttons, stainless steel screws (metric), terminal blocks, big bundle of nice 14 AWG wire (not in pic), and an odd-shaped 240 to 100 V transformer.
The Akai 4000 'solid state' reel to reel recorder. My friend plays in a band. At his place he has some nice audio gear, including a reel to reel tape machine. (He's an electronic antiques collector too, like me.) I was commenting on that, and how I've been looking for a reel-to-reel for a while. Those things were the 'elite hifi status symbol' when I was a pre-teen. My dad's architecture partner had one, and I thought it was so cool. Then by the time I could afford such things, they were obsolete. Achievement not unlocked. Now in my nostalgic years I wanted one for my 'museum', and recently happened to find some boxes of the old 1/4" tapes. Much to my surprise my friend said "oh, I have one you can have. It's broken, maybe you can fix it." Yes please!
Not that it's going to be easy to fix. One obvious problem is the right hand reel spindle tip is broken off. Also the shaft is a little bent back at the bearing so the whole reel mounting is tilted. Oh, and the reel retainer push-on caps are missing.
The shaft I can machine a new one. That tri-flange thing? 3D printer?
Another missing part is this — the capstan sleeve to use for 7 1/2 inch per second tape speed.
That's going to be a significant amount of work. Also comments on hifiengine.com suggest the transistor type used throughout this model was unreliable and should all be replaced. Hmm... In addition to all the old electrolytic caps.
On the plus side, I found the user manual and schematic, hooray.
Card index cabinets. Ha, my first thought on seeing the drawers: 'wow, now that's an obsolete information storage technology I want nothing to do with.' A moment's reframing later: 'oh, actually these are good robust drawers for components, workshop stuff, whatever.' Also, I often need bits of thin cardboard in the workshop — shims, vice jaw protectors, template cutouts, etc. So now I have a lifetime supply in a carton. Several lifetimes... Doesn't matter that they have Latin plant names written on them.
It's funny - keep these two things together, these days they are a waste of space. Separate them, and they are both useful again. The drawers fitted in well, and very thoughtfully the keys were inside.
Rather sad actually. Someone compiled a huge archive of pressed plant specimens and seeds, for which this was the index. It had all been thrown out. I was told the Melbourne botanical gardens people had taken away what they wanted, and this card index was among the dregs left behind and dumpstered. Notes on the cards suggest they were all transcribed to computer files, so OK I guess. But still someone put a lot of work into these. Now I'm going to use them as shims. Better than landfill.
The vials contained a collection of mostly 'carbonised seeds', each with a little card and species name. Another impressive effort from someone, ended up in a dumpster. I wanted the vials for general storage. I couldn't bear to just bin the contents, so I gave them a funeral pyre. With respects, and thanks for the kindling. The fire warmed my workshop for an evening.
As for the box of plumbing joints, you can never have too many of these. Especially when you are constructing a cooling water loop in your workshop/lab. I find it bizarre that someone would throw out a box of perfectly reusable bits like this. Why?
There are other reasons to question the sanity/competence of the plumbing's previous owner.
These quick-connect joints for instance. Notice the teflon sealing tape on the outer threads? Whoever did that was plain retarded. The seal is the O-ring. Even if that was leaking, the threads still don't form a seal since fluid can bypass them via the seam in the right hand part. That isn't any kind of seal, it's just a rotation separation.
The Ultrasonic Interferometer (For Solids) Another 'bottom of a dumpster' find, hence the dinged case. But so fascinating! There are no connections other than what you see on the front. Also that multi-turn dial is a very old style, that I last saw on a bit of ancient BWD equipment that contained valves. Whatever could be inside this box?
Oh. Well that's... underwhelming. But amusing. A circuit with a few resistors and capacitors, maybe two transistors, was so special it had to be epoxy encapsulated for secrecy? Home made PCB, hand soldered, hand-written lettering (and why is "1841" there twice?)
The 'mounting' was a bit of thin tinplate that might have been cut from a tin of beans. I especially like the way the wires' insulation got pinched flat by the potting case edge against the metal backing plate. Also yay spaghetti-wiring, no shielding, etc.
I'd guess this was produced a long time ago, by some very small startup. One guy? Everyone has to start somewhere.
Anyway thanks 'Mittal', for the antique dial, nice Bourns multi-turn pot, and three BNC connectors.
The Hot Air Furnace was also made by Mittal. Presumably more recently. I opened it up with some curiosity, wondering if they'd improved their act.
A: No, not really. Still crap. Looks like the 'failure mode' is that the air feed fitting has come loose from the teflon air inlet to the base of the hot chamber. Because the teflon part was never threaded properly. An easy fix. The air pump (which appears to be a small fish pond aeration pump) does work.
However the entire thing is shonky in every way. Not going to bother making a list, I'll just get it working and see if it's useful for anything. Maybe not. For instance the temperature sensor is that rod projecting into the middle of the hot chamber. I bet that is a big nuisance. Also according to the front panel it only goes up to 300° C. Really too low to work as a hot air solder reflow oven for small circuit boards.
There's obviously a missing lid, but I'd expect a block of insulating firebrick will do that job.
The plastic bags are a mystery — why would someone throw a hefty bundle of huge, brand new, heavy duty bags in a dumpster? Well, thanks anyway.
The flask heaters, I didn't look at yet.
OK, that's the Space Junk out of the way, one little roadsign joke before we get back on topic.
This was from the drive down to Melbourne. Click for the original photo.
Kind of a programmer's joke. If you like Microsoft and don't get it, never mind.
The Vacuum Pump
We came across this while walking through an interior courtyard, that is used as a rubbish dumping area by various departments in the building. Immediate impressions:
- It's been left out in the rain for a while, with both inlet and outlet ports open to the rain.
- 'Cause of death' is obvious. There's an electrical safety tag stuck to it, saying "Test status: FAIL". The kiss of death, in an environment where no one ever bothers to try and fix anything. Government funded, just buy a new one. Another attitude reveal is that it failed test back in 2012, and finally now in 2017 someone gets around to throwing it out. It has only been out here for a few days, or my friend would have noticed it before.
- It has a KF25 inlet port, and the mains inlet is a standard IEC connector. I instantly like this pump a lot.
It's a Javac model DD 150; a nice looking, relatively modern unit. Chances are high that whatever is wrong with it is simple yet no one felt like even trying to fix it.
I on the other hand, enjoy repairing things. In cases like this I get a buzz from thinking of some of my past taxes paid, coming back to me. We tossed it in the back of my car. Along with those two flask heaters that were also sitting in the rain right beside the pump.
Disclaimer. In all the following, don't assume I know what I'm doing. I actually am just guessing about pretty much everything. I've never been able to find any documentation at all by any rotary vacuum pump maker, on how to refurbish such pumps. Secretive bunch. Don't you love capitalism and the throw-away culture?
Anyway, if you try to repair your pump and break it or hurt yourself, don't blame me.
Also be aware, with vacuum pumps where you don't know the history of what they were used for, you should treat the oil as potentially poisonous and avoid skin contact.
Back in Sydney, the first thing I did was to hunt the cause of that safety failure. Worst case would be an insulation failure in the motor windings.
Opening the junction box on top of the motor, there's a surprise. Oh, splendid design Javac! They had two large mains-rated capacitors, a motor start module, and a thermal cutout unit to fit inside the box. So they wired them together, stuck some foam tape around the capacitors, and shoved them all loose into the box.
Also there is some gunky brown glue used to hold a sheet of urethane foam on the box lid, and smeared down the inside of the base box for some reason. That glue I know goes conductive over time, and urethane foam degrades as well as gathering dust. All potentially forming electrical leakage paths.
With the way there are multiple electrical lugs and exposed solder joints in close proximity here, able to move around a bit, with somewhat conductive glue and dust being blown in via a large opening into the motor interior, I'd be surprised if this didn't fail Earth leakage tests.
After a quick dust clean-out, scraping off that brown glue, a bit of wiring rearrangement, and adding a sheet of insulation between the electricals and that urethane foam 'hold down', I tested with a multimeter. No leakage apparent. It's not a high voltage leakage test, but good enough for my satisfaction.
Powering it on briefly, it runs. No Earth Leakage breaker cutout, good. But by now I'd noticed something else — the pump's oil drain plug is absent, and there's no oil in the pump. I'd missed noticing that when loading it in the car. Fortunately the oil was well drained by then, so none ended up on the cargo compartment mat.
1. In any case, it's had rain get into it, so has to be opened up. First step, separating from the motor. And what's that solenoid valve for? I've never seen a vacuum pump with something like that, not that I've seen very many. Well, remove it now, and no doubt its purpose will become clear later.
2. The internal pump body has some outside surface rusting, but not too bad. This is not from the brief rainwater exposure, it's from years of pumping something like water vapor. Internally it's good; no visible pitting just a bit of discolouration.
3. Heh. It's a 'Laboratory Deluxe series'. Except Javac have zero data about it on their web site. No manual, no service manual, the model number doesn't even give any result in their site search. Another company that pretends they never made anything more than a few years ago.
The open threaded hole at bottom right is where the oil drain plug should be but isn't.
4. Making a drain plug. It's an M12 1.5mm pitch thread. I bought a steel bolt about 3cm long. Cut off excess length, machined the thread root down slightly on the lathe. Can't use a copper washer since the case has tough dimpled enamel right up to the thread. So found a stiff neoprene tap washer that is a good OD: 19mm. Punched center hole 11mm.
5. New plug in place.
1. More visual checking. A little pitting on the outside of the pump body doesn't matter. Things to look far are the state of the cast aluminium body, inside and in the vacuum inlet. This one is very good, with no sign of corrosion of the aluminium. Other failure points are the gas one way valves, which are small flaps of rubber with spring steel backing. The rubber gets stiff and cracks, the steel corrodes. Hopefully the rubber should be a fairly chemically tough kind, like Nitrile rubber or Viton fluroelastomer. Here the flaps are the rectangular things held down by philips head screws.
2 - 4. These flap valves superficially look like they are still working, though the springs are rusty. There's a little fluff on everything from wiping oil off with tissues. This will all clean off later.
5. Disassembled, and still looking quite good. The springs for the first stage rotor vanes have no visible wear at all. The second stage vanes have no springs, just using centrifugal force to push them outwards.
1. The body parts are outside rust stripped on a bench grinder with a big steel wire wheel, taking care to not abrade the flat mating surfaces of the pieces. Then the faces have the light staining removed by polishing on fine wet&dry emery paper, resting on a slightly soft flat surface. Here I'm using a bit of softwood ply as backing. The piece is moved in a circular motion, also rotating it to get even wear across the surface. I used 800 grit. Not trying to get a mirror finish, just remove the surface staining. The oil will seal fine scratches. For the cylindrical rotor body I used the emery paper held on a cork sanding block.
It's also nice that all the O-rings and shaft oil seals seem in good condition. So I'm going to reuse them rather than try to hunt down all the different sizes. At least one shaft seal is a special too, probably only available from Javac.
2. Probably clean enough.
3. The cast aluminium end plate also cleaned. This took a fair bit of scrubbing with stainless steel wool, held in forceps to get into nooks. Using kerosene as a wash fluid, and wiping 'clean' with old rag bits, also in forceps. All of the gunge seems to be hardened rust sludge and stains adhering to the alloy, rather than corrosion.
4. A trial assembly. At the moment just to get it in one piece for protection, and to check I remember where everything goes. All the parts are wiped with a thin coat of pump oil, though I know I will be stripping it again before final assembly. This time the oil is so the shaft can be rotated by hand to check for binding, and to prevent rusting if I get sidetracked and leave this project hanging for a while. Gosh, that never happens, does it?
5. See that little light coloured aluminium hexagonal thing? It's a simple one-way valve, apparently meant for oil. And I have no idea what it does. In fact there are several features in the interconnecting channels in this pump I don't understand. Something else I want to do when it's apart again, is draw a diagram of them and try to figure out why each one is there.
1. A yellow five gallon drum. Also a face palm moment.
When I was given a bunch of vacuum gear including the large chamber, many years ago, this drum was offered too. I was told that it contained vacuum pump oil. Great! Pump oil is apparently quite expensive, so that would be very convenient. For various reasons (mostly being repeatedly clubbed over the head by Life) it's taken a long time to get the vacuum system project to the point where I'm installing vacuum pumps. All that time this drum has sat around in my workshop awaiting its day. I never could find any data online about Shell "Vitrea Oil 41" to verify it was actually compatible with vacuum pump use.
When assembling this pump, I needed a small amount of oil. Rather than use some of the few small containers of known quality vacuum oil I have, I thought I'd use this stuff. First thing, I should check the viscosity is at least in the right range. Lugged the drum over from the shelving area, opened lid. Hmm, that's funny, it has a smell. Vacuum oil should have low volatiles, ie little smell. I sucked up some into a syringe. Err... that's even more odd, it has very low viscosity, judging by the rate a bubble moves back and forth when tilting the syringe. Also that colour... looks a lot like petrol. Takes a better sniff. Smells like petrol too.
I squirted a small amount into my (empty) wood burning workshop heater, lit it. Whoomp!
Sigh. It actually is petrol. Very old, but still has much petrol-nature.
I was given this drum in early 2000s. The guy who ran the particle accellerator and gave this to me had forgotten it wasn't actually 'Vitrea 41', so it must have been sitting around there for long while. It's at least 20 years old.
Anyway, two things. One, I've had an old, little bit rusty, thin metal, nearly full 5 gallon drum of petrol sitting in my workshop for maybe 15 years. Not far from a wood-burning heater. Two, I don't have a five gallon drum of vacuum pump oil. Rats.
2. The flap valves disasembled. Darn, they actually need replacing. Both rubbers, and definitely the 2nd stage springs which are badly pitted.
3. Curiously the 2nd stage rubber flap is cracked on the outer side, like this. While the larger 1st stage rubber is not cracked at all. I'd have thought the 1st stage one would be mechanically stressed more?
4. A cable pass-through slot. Originally it was too small and the plastic sleeve could not be stuffed into it, so was crimped. I filed it a bit larger.
5. By now I'd figured out what that solenoid valve is for. It's cool! This pump has an air-actuated piston valve on the suction inlet, to prevent oil being sucked back into the vacuum system when the pump is turned off. This valve is energised all the time when the pump is running; blocking air inlet to the pump-side of the valve piston, thus keeping the inlet line open. When power goes off the valve opens, lets in air, closing the inlet valve and admitting air into the pump interior. Nice! I wish all my pumps had that feature.
1, 2. The flapper rubbers are 2.4mm thick. Here's a bought offcut of 2.4mm thick nitrile rubber. ($50 from Associated Gaskets, Revesby.)
Cut a little piece off to keep in the workshop, the rest to be packed away in a bag in storage. (Yes, one of those big plastic bags. Useful already.)
3. Using a paper guilotine to cut clean straight edges.
4. New flaps cut.
5. Punching the holes. The closest hole punch I have is slightly undersize for the aluminium spacer rings, but hopefully it doesn't matter.
On Monday 20170828 I phoned Javac's Sydney office with a few questions about their model DD150:
- Are there User and Service manuals available in PDF?
- Cost of a flapper valve spring set?
- Cost of an O-ring set?
- When assembling the stack, what's the rule/method for setting the rotor to body clearance?
My guess is "As close as possible, without binding."
- If I was able to talk with someone who knew the answer to the clearance question, then maybe they'd also be able to answer this: Is the springiness and curve of the flapper springs critical?
Actually I wasn't expecting much joy with any of that. Long experience with the way such companies work. Call me cynical... but I was right. The result was:
Manuals: The guy said he'd look, asked my my email address, then after virtually no 'looking' time announced they had none. "That pump was made around 15 to 20 years ago, sorry we don't have any manuals." Also they do not stock
any spare parts for such 'old' models.
So that was a big zero on most of my questions. I asked about the rotor clearance thing anyway, just for a laugh. He went away for a few moments. Came back with an answer: "One thou, but there's a jig required."
Ha ha ha, still working in Imperial units, are we? But at least it's a number. I thanked him, didn't bother to ask about the spring stiffness.
Well, it was worth phoning them, even though the outcome was as expected. Now I'm certain I'm on my own with refurbishing the thing, rather than just expecting this but suffering a niggling doubt that I'm maybe being too negative.
1. The original flapper springs are 0.25mm spring steel. Which I don't have, and last time I tried to buy thin sheet spring steel I didn't have any luck at all. Couldn't find a local source. I did find a US source who do online orders, and their form accepts overseas addresses and calculates postage, but after placing an order I received this email:
From: "McMaster-Carr"
To: ...me...
Date: ...back in 2002...
Subject: Your order on our website
Hi .....,
Due to the complexity of U.S. export regulations, McMaster-Carr accepts international
orders only from our established customers. This decision also applies to orders
shipping within the United States, because it is based on the final destination of
the items. We cannot accept this order or future orders.
Ha ha ha... Way to go, red tape demons!
I should retry now, to see if things have changed. Or use one of the USA 'assisted purchase' channels that now exist, specifically to bypass this rubbish. Or try to find a Chinese source, where there's no such bullshit.
But that will take weeks, and may have no result. In the meantime I'll try some 0.3mm stainless steel springy sheet I do have. Can always make something better if this doesn't work out well. Here I've just cut a small strip off the roll, for convenient working. That big roll really wants to go SPROING, and making sure it doesn't is a bit tricky. Think large coiled clock spring with sharp edges.
2. Spring pieces cut. It's easy enough to cut the straight edges without distorting the metal, by holding the snips so all the 'curl' goes into the offcut piece.
Not so easy, is making a neat hole in thin sheet metal. You can't just drill it, as when the drill bit bites in it pulls the metal edges upwards. Also the hole won't be round. The industrial way to make precision thin metal pieces like the original springs, uses photo-resist chemical etching to eat way unwanted metal, making many pieces at one time and not distorting the sheet at all. I can't do that.
So, making a few holes in these little sheet springs will be the most involved part of this whole project. I'll have to make a jig for cutting clean holes in thin sheet metal. Actually It's something I've meant to do for a while, and it will come in handy for other things. Hence not such an inefficient effort.
3. The idea is to very firmly and evenly clamp the sheet right at the edge of the hole, so it can be drilled without distortion. This means the clamp has to be very strong and have matching and perfectly lined up holes on both sides of the sheet.
Here I'm starting with two bits of 19mm square steel cut from bar stock.
4. With the two bars lined up and clamped, drilled a couple of pilot holes. These are where alignment pins will go. The pins will be cut from that bit of polished steel rod (from the box of rods salvaged from photocopiers.)
5. All the alignment and clamping stuff done. One small oops — only after I'd drilled the first full size alignment-pin hole right through, it occured to me that I could leave a bit of metal at the outer ends of these holes, so the pins couldn't fall out.
1. Jig completed. I only needed two hole sizes for this work, but gave it four sizes: 3, 4, 5 & 6mm.
2. The big moment. Try making a hole in the spare bit of sheet metal. Will it work?
3. Yep! Perfect. I'm happy.
4. Drilling the actual flapper springs. The extra difficulty is getting the hole in the right place. I just made a slight dimple in the center of the marked hole outline with a light tap on a center punch, with the sheet springs resting on hardwood. Then looked down the alignment hole to get the dimple in the center, before tightening the clamp bolts. Works accurately enough. Also I drilled the flappers in pairs.
5. Last and most inaccurate — cutting that little slot using a thin abrasive disk in an engraver. By eye and hand, so it wasn't all that great. But good enough.
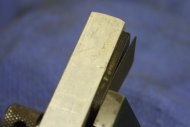 |
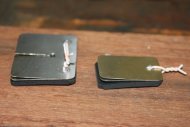 |
1. Another small but probably important detail. The original springs are not flat. The one against the rubber flap is bent down against the rubber slightly, and the upper one is bent away from the rubber and lower spring. Like this.
2. Well, I'm using a different type of material (Hard stainless steel instead of tempered high-carbon spring steel), and different thickness (0.3mm instead of 0.25mm) so there's not much point trying to be extremely exact about this. I just bent my replacement springs to roughly the same shape, by eye. Also the new rubber has a curve, which I'll assume should be oriented 'down'. Fingers crossed.
Anyway, now the orientation of the pieces matters. So they are held together with bits of wire till they are mounted.
Time Bites
Here the intended 'quick vacuum pump rebuild' seemed to be going well, so Time decided to sink its teeth in. Teeth in the form of a series of non-maskable interrupts; some mundane, some calamitous:
- A few weeks ago my car went out of rego, due to needing some maintenance to pass inspection. Work which I can do, but I decided to do more than just the one relatively minor rego sticking point (a torn front wheel CV joint rubber boot.) A bunch of other work I'd been putting off. Which has kind of blown out in schedule, due to other interrupts. See NobLog — Car Grafting. Fortunately I have a backup car, so my car being out of action is no great inconvenience. But can't be left too long, or re-registering it becomes an issue.
- On 14th August an old friend passed away after years of illness. Vale David Spicer.
- Then the August Melbourne trip, third one this year. Drove down on Thursday 24th Aug, back on the following Monday, the 28th. This was for a non-optional purpose, with the equipment (and vacuum pump) as unexpected side effects. But now there are starting to be too many active chore threads...
Also, do I want to reassemble this pump without a propper solvent cleaning? No. But I haven't yet made much progress on my project to build a vapor-phase cleaning system.
Sigh. Great. This vacuum repair project has now been buried on my workbench for several months, underneath more recent, more urgent projects. Making this unfinished writeup one of several in a writing logjam.
So, even more deja vu. I'm going to post it as is now, and get back to it when the vapor-phase system is functional. Yet another unfinished project and its Noblog article.
To be continued...